What does explosion proof mean?
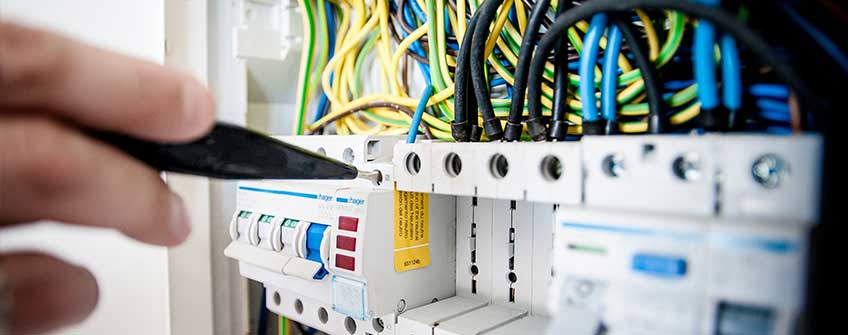
To understand what is meant by explosion proof, we must look at the context of the term and the organization that defined it. The National Fire Protection Association (NFPA) began publishing the National Electric Code (NEC®) in 1897. The NEC® is also known as NFPA 70 and ANSI/NFPA 70 from its inclusion in the body of NFPA codes.
The NEC® includes definitions for several types of protection techniques acceptable when designing products for use in hazardous (classified) locations: Explosion proof, dust ignition proof, dust tight, purged/pressurized, intrinsically safe, and hermetically sealed. These definitions set the criteria that must be met by all components installed in hazardous (classified) locations.
To meet the criteria for the explosion proof rating, an enclosure must be able to contain any explosion originating within its housing and prevent sparks from within its housing from igniting vapors, gases, dust, or fibers in the air surrounding it. Therefore, explosion proof, when referring to electrical enclosures, does not mean that it is able to withstand an exterior explosion. Instead, it is the enclosures ability to prevent an internal spark or explosion from causing a much larger blast.
Additionally, the NEC states that equipment must meet the temperature requirements of the specific application in which it is to be installed. This means that the operating temperature of the motor (and its enclosure) or other component cannot be greater than the lowest ignition/combustion temperature of the gases or dusts in the atmosphere where the component is to be installed.
All components are labeled on their nameplate with the distinct classification in which they have been tested and approved for installation.
How are the protection techniques rated?
Each of the protection techniques mentioned above is permitted for use only in very specific applications. For example, components and equipment complying to the dust tight specification are approved for use in Class II, Division 2, or Class III, Division 1 or 2 locations, while those listed as explosion proof are approved for use in Class I, Division 1 or 2 locations.
Often, those products listed for a higher classification surpass the requirements for lower classifications. In fact, the NEC® explicitly states “Equipment that has been identified for a Division 1 location shall be permitted in a Division 2 location of the same class, group, and temperature class,” thereby complying with requirements for the Division 2 areas [ANSI/NFPA 70:500.8(A)(2)].
Who tests Explosion Proof equipment?
Nationally recognized testing laboratories such as Underwriters Laboratories and Intertek use marks to denote that the products they have tested conform to the standards set by the (NFPA) and by other international standards organizations. These marks, which include UL, CSA, ETL, and others, can be looked for to determine compliance with the standards. Products that do not bear these marks may not meet the requirements of the NEC.
A ready for production prototype is sent to a testing laboratory. Once approved, that laboratory sends inspectors to the manufacturer on occasion to ensure that nothing has been changed in the design or manufacturing of the component.
Specific Systems® are engineered to perform
Unlike systems sold by HVAC modifiers, units fabricated by Specific Systems® are engineered from the sheet metal to the compressor choices to meet the standards laid out in the NEC®. Specific Systems® uses only fully approved and labeled components and wiring methods on all systems.
- Hermetically sealed scroll compressors in every unit
- Standard totally-enclosed, fan-cooled (TEFC) motors
- Class I Div 1 hazardous duty motors, when specified
- Electrical control panels built in our UL 508A approved electrical shop
- CSA C/US approved explosion proof compressors
- UL Listing and CSA C/US Approval of all InPac® and AirPak units
- All wiring is properly routed through conduit and labeled in order to exceed NEC® standards
Some refineries and processing facilities operate in cooler environments. Because of the often cooler ambient temperatures, heat is often required in these applications. However, typical open coil heaters can not be used in hazardous areas due to the explosion hazard. For these applications, explosion proof fin tube heaters must be utilized.
Explosion proof heaters incorporate fin tube heating elements and enclosed electrical connections to meet code and reduce surface temperatures. Specific Systems® explosion proof heaters are CSA C/US approved.
Additionally, explosion proof crankcase heaters are used in these conditions instead of standard crankcase heaters.
Depend on Specific Systems®
Specific Systems® has been building HVAC and pressurization units for hazardous (classified) areas since 1974, and is the oldest and largest manufacturer in the industry. Because we build the units, we will be here to assist with any questions you have post-installation.